March 15, 2024 — Marking International Consumer Rights Day, DALY hosted a Quality Advocacy Conference themed "Continuous Improvement, Collaborative Win-Win, Creating Brilliance", uniting suppliers to advance product quality standards. The event underscored DALY’s commitment: "Quality is action, not words—forged in daily discipline."
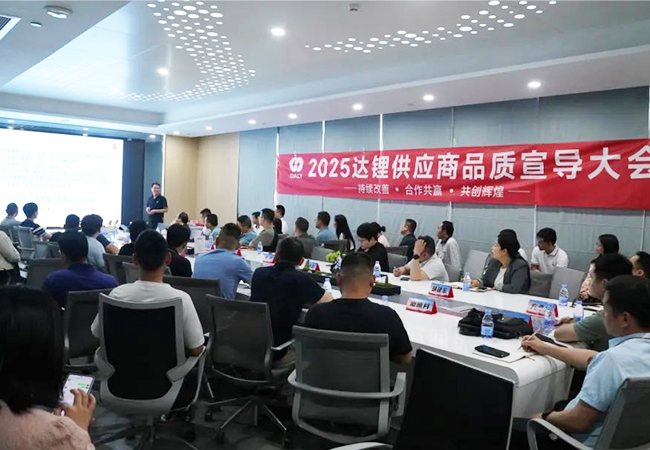
Strategic Partnerships: Fortifying Quality at the Source
Quality starts with the supply chain. DALY prioritizes premium raw materials and components, enforcing rigorous supplier selection criteria—from production capacity and ISO compliance to delivery performance. Evaluations allocate 50% weight to product quality, with a non-negotiable IQC (Incoming Quality Control) batch acceptance rate (LRR) exceeding 99%.
To ensure accountability, DALY’s quality, procurement, and technical teams conduct surprise factory audits, inspecting production lines, storage practices, and testing protocols. "Onsite transparency drives faster solutions," a DALY representative noted.
Ownership Culture: Quality Linked to Accountability
Within DALY, quality is a collective responsibility. Department leaders’ performance metrics are tied directly to product outcomes—any quality lapse triggers immediate accountability measures.
Employees undergo continuous training on cutting-edge production methods, quality systems, and defect analysis. "Empowering every team member as a ‘quality guardian’ is key to excellence," the company emphasized.
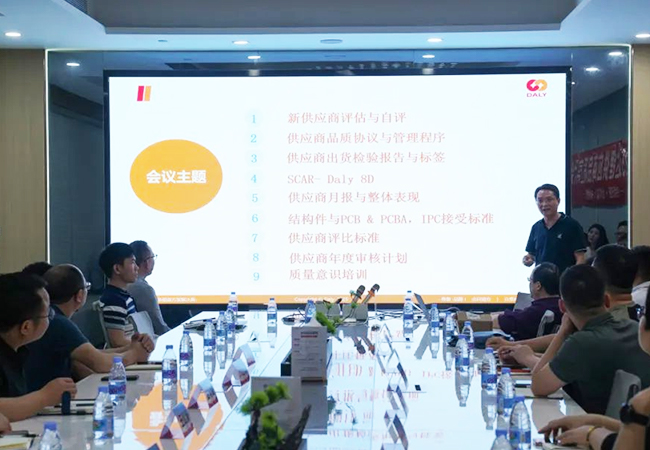
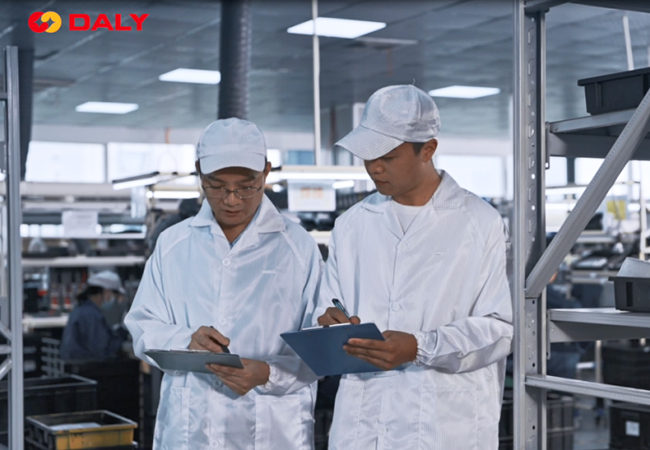
End-to-End Excellence: The "Three No’s" Principle
DALY’s manufacturing ethos hinges on three mandates:
- No defective production: Precision at every stage.
- No acceptance of defects: Inter-process quality barriers.
- No release of defects: Triple-check safeguards (self, peer, final inspection).
Non-conforming products are isolated, tagged, and reported instantly. Detailed batch records—tracking equipment, environmental data, and process parameters—enable full traceability.
8D Solutions & Zero-Error Discipline
For quality anomalies, DALY deploys the 8D framework to eliminate root causes. The "100-1=0" rule permeates operations: A single flaw risks reputation, demanding relentless precision.
Standardized workflows (SOPs) replace human variability, ensuring consistency across teams, even for new hires.
Progress Through Partnership
"Quality is a relentless journey," DALY affirmed. "With aligned partners and uncompromising systems, we turn promises into lasting value for customers."
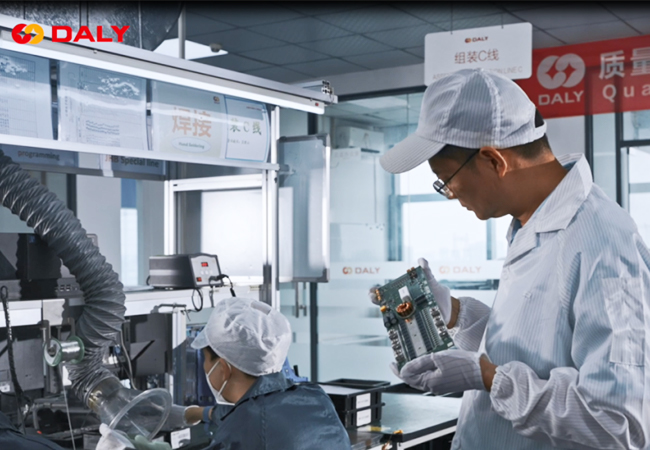
Post time: Mar-17-2025